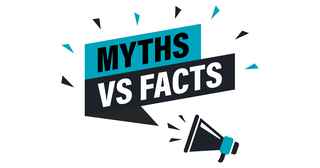

Architectural panels of today are significantly improved from a decade ago. Advancements in prefabrication, technologies, architectural finishes, manufacturing techniques and assembly processes have exponentially increased the functionality, creating lightweight, value-adding building enclosure products.
Unfortunately, several misconceptions about integrated scope prefabricated building envelope systems like Infinite Facade™ are keeping architects from tapping into their full potential. A reliance on traditional building methods and an unfamiliarity with prefabricated systems continue to impede widespread adoption.
But as innovative architectural firms start specifying these new products and implementation momentum builds, these fallacies are being tested and disproven on projects across the U.S. Let’s take a look at some of the myths that we are hearing related to Infinite Facade:
Myth: Infinite Facade is new, with limited “real-life” testing – The lightweight building technology and the way it is manufactured – thin shell on metal frame – has been around since the early 1990s. Since that time, the product was engineered to what is available today. During the product development, it was exhaustively tested for fire resistance, thermal performance and permeability, among other things, and it meets or exceeds ASTM standards regardless of region or application. Additionally, there are hundreds of thousands of sq ft of the product service every day.

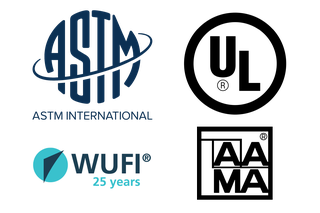

Myth: Infinite Facade can only support small punch window openings – With advancements in engineering and manufacturing efforts, traditional precast can now achieve much larger window openings than the past. Infinite Facade takes this to the next level, by using a tube steel frame in place of structural concrete, enabling it to support large window-to-wall ratios. Infinite Facade comes in three variations – the 75, 85 and 100 series – each denoting different window configurations. The panel-to-panel joints are also less conspicuous. In the 75 Series, the horizontal panel-to-panel joint is situated in the opaque surface above and below the window; in the 85 Series, that joint is at the head of the window; and the 100 Series offers full-height glass with the integration of spandrel glazing at the head and sill to cover the slab edge and frame members.
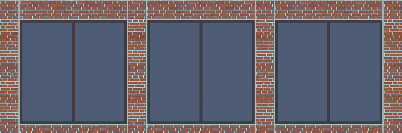
Infinite Facade 75
Utilizes standard size window openings.
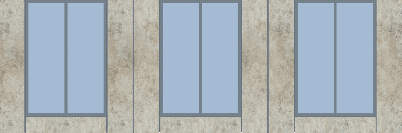
Infinite Facade 85
Utilizes window openings that align with the top of the panel, minimizing horizontal joints.
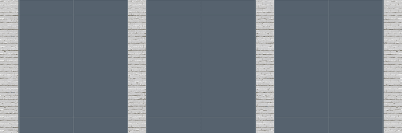
Infinite Facade 100
Provides full height, continuous exterior glass.
Myth: Architectural designs are limited by prefab capabilities – The architectural community is trending toward more variation in their façade designs, such as the introduction of opaque finishes, which offer more depth for natural shading and other unique and distinctive design features. Projections and faceted designs are very cost effective when incorporated into Infinite Facade's design in lieu of traditional site-built enclosures. However, many times architects don’t feel that lightweight prefabricated products can affordably achieve their design intent. On the contrary – this is an area the product excels in, allowing designers to choose from infinite possibilities of color, finish, textures and material combinations. You don't have to select just a single finish. With the flexibility of the design capabilities, when consulted early – prefabricators can often guidance on how to accomplish the objectives of design and cost.

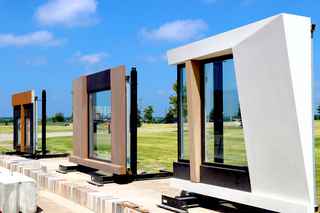

Myth: Infinite Facade is only an exterior architectural opaque finish product – In simplest terms, Infinite Facade is everything for the enclosure of the building, but the drywall. Arriving at the site with completed finishes, factory-installed insulation, factory-installed windows, pre-engineered steel frame and drywall-ready accessories, it supports the fastest building enclosure on the market. That provides tremendous value and risk mitigation for owners and project teams. On average, Infinite Facade brings together the scope of up to seven subcontractors and combines warranties into a single-source. Additional benefits are streamlined coordination, increased quality control over reduction of labor required on site and an accelerated project schedule.

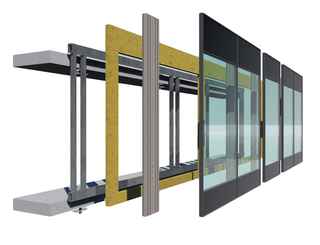
Myth: Prefabricated products featuring precast can only achieve a gray, industrial appearance – Today’s precast architectural panels come in a variety of colors and finishes, as well as incorporate materials such as cast-in thin brick, stone or terracotta. One of the newer offerings – a simulated metal panel finish – is generating a lot of buzz in the design community. The precast is treated and finished in a way to give the appearance of a metal panel, while being more cost effective and more durable.
Additionally, the prefabricated designs of today aren’t confined to a single color or finish with a flat facade. A mix and match of different colors, materials and panel skin articulations can create a unique design, with both efficiencies and affordability. Also, the panels have the ability to achieve 3D shapes and forms to support virtually any design intent.
Myth: Spray foam insulation applied in the field is just as effective as in a climate-controlled prefab plant – Many manufacturers recommend temperatures of 40 degrees or higher for ideal spray foam product applications, and in many geographies that’s just not possible during the winter months. Fortunately, it’s always sunny and 75 degrees in a prefabrication manufacturing facility. Having the panels insulated before they arrive at the site also minimizes jobsite labor, additional trade partners, construction schedule and risk at the site, ultimately enhancing safety.
Myth: Infinite Facade requires an electrical furring wall to be built on site – Infinite Facade comes with a “drywall-ready” frame with no need for additional site-built furring walls.
Myth: Installing windows at a prefabricator’s facility could cause the windows to be broken during transit to the site – Actually, pre-installed windows are better protected during shipment as they are properly attached to the substrate versus sitting on a pallet.
Myth: Lighter weight wall panels don’t impact deliveries or crane sizing – In reality, up to eight Infinite Facade panels can fit onto one truck (as compared to only one or two for traditional precast), reducing impacts to the site and enabling the prefabricator to transport greater distances. The panels enclose the building at lightning speed, while the lighter weights enable the use of a smaller tower crane, resulting in cost savings throughout the project.
Myth: Infinite Facade can’t be used in conjunction with other materials – Infinite Facade was developed to be used with a variety of superstructures from Cast-in-Place to Steel to Precast. It also “plays nice in the sandbox” with other façade systems, whether that be curtainwall, window wall or a host of others. The Infinite Facade preconstruction teams help design partners work through the project coordination and detailing.
Myth: A complete set of contract documents are required to begin discussions on price and schedule – With only some basic information, we can generate a price, schedule and a proposed panel configuration without even looking at a drawing.
Ultimately, a lightweight prefabricated system such as Infinite Facade can be a true game-changer for design and construction professionals. Regardless of project type, parameters or budget, it’s never too early to ask a prefabricator to help you achieve your design intent.
What is Infinite Facade?
One of the latest advancements in prefabrication is integrated scope cladding solutions, like Infinite Facade™; a single-source prefabricated building envelope system, that streamlines facade design and construction. The system blends the extensive architectural capabilities of a thin, lightweight precast exterior with a steel frame, insulation, and pre-installed glazing, arriving on-site as a complete unit, immediately enclosing the building, and significantly expediting project schedules.
Who manufactures Infinite Facade?
Facades Consortium Group LLC is a partnership between Wells and Clark Pacific to facilitate and accelerate the R&D efforts surrounding Infinite Facade. Both companies are aligned in the vision to evolve lightweight panel systems to create a resilient, durable, and sustainable built environment. We are committed to designing, manufacturing, and installing a quality product no matter where the project is located. Infinite Facade is engineered to be flexible to meet regional building and design requirements.
Interested in learning more about Infinite Facade™?