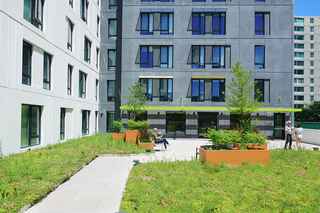

Tackling Sustainability with Lightweight Building Enclosures
Today's architectural landscape demands buildings that are not only visually stunning but also environmentally responsible. Design teams are constantly looking for new finish offerings and meticulous detailing. Contractors are demanding more offsite prefabricated assemblies that save time and reduce costs. Infinite Facade™ offers a single-source solution with a sustainable and complete building envelope system.
Key Benefits of Infinite Facade
Lightweight Design
- Reduced Structural Load: Infinite Facade's lightweight design significantly reduces the load on the building's structure, leading to smaller foundations and less material usage. The structural frame components of Infinite Facade are composed of structural HSS steel members in place of structural concrete.
- Faster Installation: Larger, prefabricated panels can be installed more quickly, accelerating construction timelines.
Energy Efficiency
- High-Performance Insulation: Advanced insulation technology minimizes heat loss and gain, reducing energy consumption. The insulation selected specifically for Infinite Facade is energy-code compliant and has one of the highest available R-value ratings per inch.
- Continuous Insulation: Eliminates thermal bridges and cold spots, further enhancing energy efficiency.
Sustainable Materials
- Reduced Material Usage: The thin-skin design and prefabrication process minimize material waste, utilizing concrete by over 70% compared to traditional precast panels. Additionally, simulated finishes such as stone and metal panel eliminate the need for additional materials in their entirety.
- For example, a normal masonry brick veneer is 3 5/8” thick, whereas a thin-brick veneer is only ½” thick. That’s an over 85% reduction in raw material consumption.
- Recycled Content: The insulation used in Infinite Facade contains a significant amount of recycled material.
Prefabricated Components
- Faster Construction: Prefabricated panels and components are manufactured off-site, reducing on-site labor and accelerating construction timelines.
- Improved Quality Control: Controlled factory conditions ensure consistent quality and precision.
- Improved Safety: Windows are preinstalled at ground level, reducing the need for lifts, scaffolding, or hosting and increasing the safety of the installers.
- Reduced Waste: Minimized material waste and efficient logistics contribute to a more sustainable construction process.
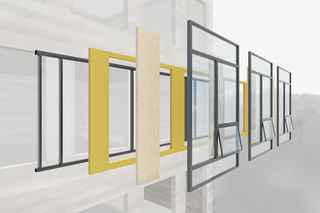

Through its use of a steel frame, Infinite Facade can achieve higher window-to-wall ratios than ever. The structural frame also acts as a drywall-ready substrate, eliminating the need for additional furring walls while reducing the material, time, and labor required on site.
By combining innovative design, advanced materials, and efficient construction techniques, Infinite Facade delivers a comprehensive solution for sustainable building envelopes. With its focus on energy efficiency, reduced environmental impact, and accelerated construction timelines, Infinite Facade is setting new standards in the construction industry.
Interested in learning more about Infinite Facade?
Learn more about Wells sustainability practices.
