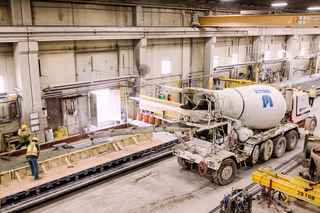

By Doug Woltmon & Jessica Faulkner
Offsite Construction Drives Efficiency and Control
Efficiency is the name of the game in construction. Unfortunately, many project teams often fall short of the goal – nearly 90 percent of large-scale projects are delivered late, and nearly 60 percent up to two months late, according to a recent analysis by New Civil Engineer magazine.
For those and other reasons, taking work off-site is becoming an increasingly attractive solution to the efficiency problem, as it provides project teams with greater control over labor, quality, safety, schedule and ultimately cost while supporting owners with accelerated occupancy.
Many architects and engineers are incorporating prefabricated components into their designs, since offsite prefabrication is a “lean” process and offers significantly more control over quality and productivity than the typical jobsite. In fact, these manufacturing facilities, incorporate multiple layers of quality control into their processes and eliminate the start and stop characteristics of a jobsite.
A single-source facade solution.
Additionally, technology has enabled prefabricators to significantly expand their design palettes and integrate a variety of finishes such as metal, brick, stone, terracotta, accent colorations, exotic stains or other architectural features previously performed by other trades. One of the latest advancements in prefabrication are integrated scope cladding solutions, like Infinite Facade™ – blending architectural capabilities of a thin, lightweight precast exterior with a steel frame, insulation and pre-installed glazing, arriving on-site as a complete unit, resulting in an immediate enclosure on the building, significantly expediting project schedules.
With more work falling under the prefabricator’s “umbrella,” it provides the project team with a single point of contact rather than having to juggle multiple subcontractors and suppliers, ultimately reducing risk. Giving project teams greater control while improving project outcomes.

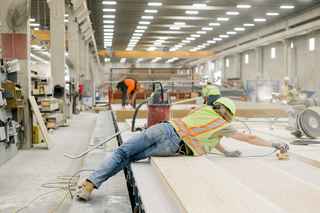

Why Project Teams are Making the Shift to Offsite Construction
The increasing popularity of prefabricated building envelope systems is grounded in partnerships that have evolved over time, where the prefabricator, owner, designer and contractor work collaboratively and transparently to find opportunities to succeed together.
Schedule Benefits
To be most effective, prefabricators are getting involved earlier in a project’s timeline, helping architects and engineers optimize their designs to fit their budget and aesthetic vision. They are suggesting efficient timesaving alternatives to ensure that designs are compatible with their manufacturing equipment and methodologies – long before changes become costly.
And by incorporating an integrated prefabricated facade, designs, submittals and approvals are completed much earlier in a project’s timeline. That enables prefabricators to be proactive rather than reactive to supply chain issues and other costly delays that are so prevalent today.
The schedule benefits, as only panels that are scheduled to be installed that day are delivered via just-in-time delivery, significantly reducing onsite storage needs. These panels are subsequently installed and detailed by the prefabricator's trained field crews, often limited to just 4-8 workers on-site for the panel installation. This further diminishes clutter and congestion at the jobsite, a notable advantage when space for laydown and maneuvering is restricted.

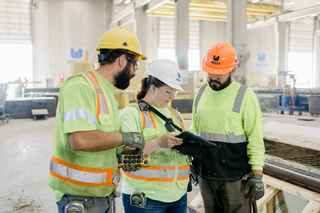

Safety
Safety is another beneficiary. The prefabricator performs daily safety walks at the production facility, and tightly manages the movement of materials. As a result, it reduces site impact making for increased visibility and safety on site, while effectively minimizing delays.
Ultimately, prefabricated building envelope systems that are manufactured off-site provide certainty when it comes to concerns with schedule, quality and execution.