Innovative solutions.
Located in Wheat Ridge, CO, Intermountain Health Lutheran Medical Office is a five-story medical office building within the Lutheran Hospital campus services patients in the greater Denver area. The medical office building boasts a modern exterior, featuring large-format panels with preinstalled windows, clean, straight reveals and an architectural gray acid etch finish that shimmers in the Colorado sun. Additional finish elements include site-built curtain wall, metal panel, and hand-laid stone to complement the Infinite Facade panels, further enhancing the overall building design aesthetics.
When selecting the exterior materials, the design team was challenged with finding a building envelope solution to meet the project goals without requiring structural redesign. Wells introduced the concept of Infinite Facade™, a fully unitized building envelope system. The project team quickly adopted Infinite Facade due to its lightweight nature; it could be implemented within the current steel superstructure and was able to match the aesthetic design intent. Wells was officially contracted in a design-assist capacity to support the design team through permit documents and ultimately make the project a reality.
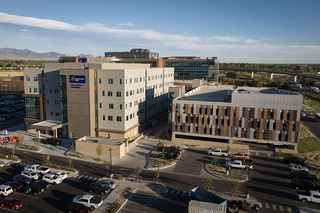

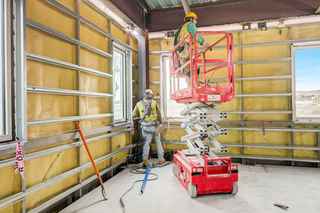
The project site proved to be another challenge for the construction team. An adjacent parking garage and healthcare campus also undergoing construction limited the amount of material laydown area available. Infinite Facade is a complete envelope system that arrives at the jobsite with windows and insulation already installed within the panels, and they can be swung into place directly from the truck they are delivered on. This drastically reduces the amount of jobsite area needed in comparison to other envelope materials. The five-story building utilized 90 panels that were erected in just thirteen days.
The Wells sealants team played a pivotal role in ensuring the durability, safety and energy efficiency of the building by providing comprehensive caulking, horizontal firestopping and panel-to-panel spray foam touch-up to ensure seamless integration and superior thermal performance. Utilizing Wells as a full-service company allowed the other trades to begin work on site in a fully enclosed building ahead of schedule.
By incorporating a single-source envelope system early in the design phase, the project team was able to better control and reduce costs through design-assist value engineering, reduce their overall schedule, keep the original structural system and enhance the original architectural appearance. Additionally, effective communication and coordination with the building partners ensured a successful project outcome. This medical office building exemplifies the power of collaborative design and effective problem-solving, all while changing the way the construction industry builds.
I would do every project with this product.
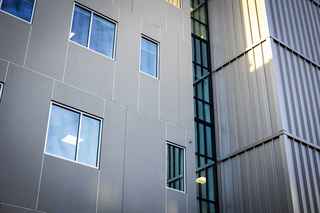
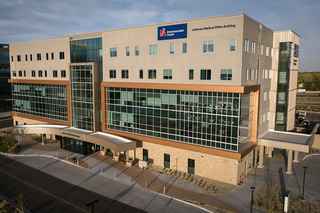

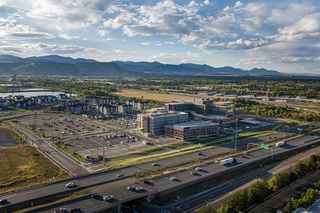