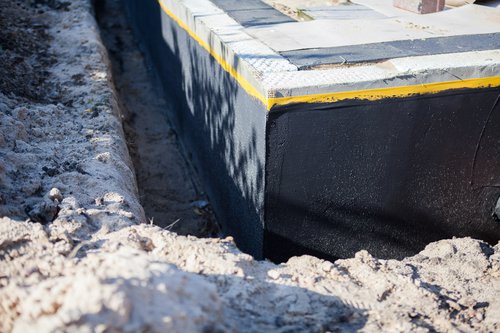
Wells sealants and restoration team are experts in commercial waterproofing. In this comprehensive guide, we will explore the importance of commercial waterproofing in construction projects, the challenges involved, and the various methods and techniques available. We will also delve into the specific topic of waterproofing concrete and highlight Wells' expertise in providing high-quality waterproofing solutions. By the end, you'll understand what it takes to protect your commercial building from water damage.
What is Commercial Waterproofing?
Commercial waterproofing refers to the process of making a building or structure resistant to the intrusion of water. It is a vital aspect of construction as water infiltration can lead to severe damage, compromising the integrity and safety of the building. Commercial waterproofing involves implementing measures to prevent water from entering through walls, floors, roofs, and other vulnerable areas. By effectively waterproofing a commercial building, you ensure its longevity and maintain its value.
Commercial Waterproofing Challenges
Waterproofing commercial buildings comes with unique challenges. Unlike residential properties, commercial structures are often larger and more complex, with multiple levels, extensive surface areas, less permeable surface and various architectural features. These factors increase the risk of water infiltration and require careful consideration during the waterproofing process. Failure to address these challenges can lead to serious consequences, such as mold growth, structural deterioration, and costly repairs.
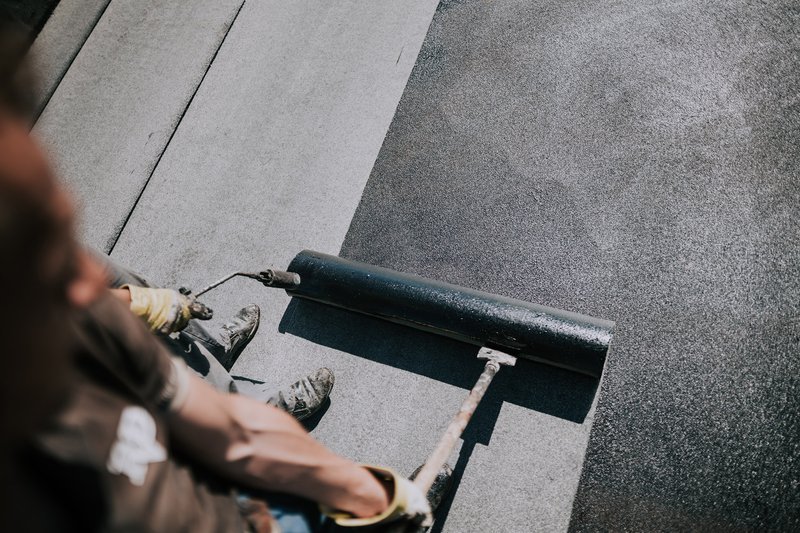
Benefits of Commercial Waterproofing
Implementing proper waterproofing measures in commercial construction offers numerous benefits. First and foremost, it ensures the safety of occupants by preventing water-related hazards and maintaining a healthy indoor environment. Waterproofing also contributes to energy efficiency by reducing air leakage and heat transfer, resulting in lower utility costs. Additionally, it extends the lifespan of the building by protecting it from water damage, which can lead to structural issues. Lastly, proper waterproofing helps preserve the property's value, making it an essential investment for commercial building owners.
Methods and Techniques for Commercial Waterproofing
Various methods and techniques are available to address the waterproofing needs of commercial buildings. Let's explore some of the most common ones:
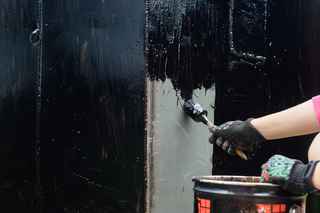
Liquid Waterproof Membranes
Liquid waterproofing membranes are applied as a liquid coating that forms a seamless, durable, and flexible barrier on the surface. They can be sprayed or rolled onto different substrates, such as concrete, metal and wood. Liquid membranes offer excellent adhesion and can be used to waterproof roofs, balconies and other horizontal surfaces.
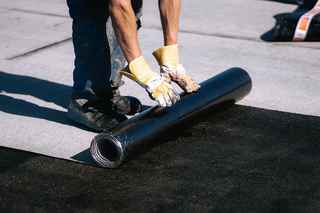
Sheet Waterproofing Membranes
Sheet waterproofing membranes consist of self-adhesive or torch-applied sheets that are applied to the surface. These membranes provide a reliable barrier against water intrusion and are commonly used for below-grade applications, such as basements and foundation walls. They are also suitable for horizontal and vertical surfaces.
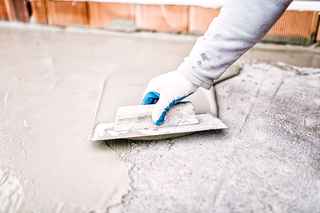
Cementitious Waterproofing
Cementitious waterproofing involves applying a cement-based coating or slurry to the surface. It creates a protective layer that prevents water penetration while allowing moisture vapor to escape. Cementitious waterproofing is commonly used for concrete structures, such as foundations, retaining walls and water tanks.
Bentonite Waterproofing
Bentonite waterproofing utilizes the natural swelling properties of bentonite clay to form a watertight barrier. It involves installing panels or applying bentonite sheets to the surface, which swell upon contact with water, effectively sealing any gaps or cracks. Bentonite waterproofing is suitable for below-grade applications and can be used in conjunction with other methods.
Drainage Systems
Drainage systems are an integral part of commercial waterproofing. They help manage excess water by collecting and redirecting it away from the building. Exterior drainage systems, such as french drains, channel water away from foundations, while interior drainage systems, like sump pumps, remove water that accumulates in below-grade levels.
Each method has its own strengths, weaknesses, and suitable applications. It is essential to assess the specific requirements of your commercial building and consult with professionals, like Wells Sealants and Restoration team, to determine the most effective waterproofing approach.
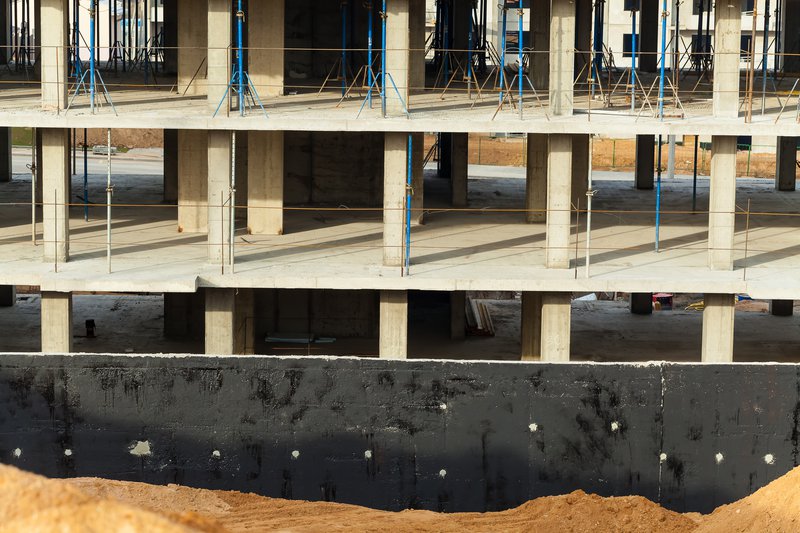
Waterproofing Concrete in Commercial Construction
Concrete is a commonly used material in commercial construction, but it is susceptible to water infiltration. If not properly waterproofed, concrete can absorb moisture, leading to cracking, spalling, and corrosion of embedded reinforcement. To combat these vulnerabilities, specific solutions and techniques can be employed.
One effective method for waterproofing concrete is the use of waterproofing admixtures. These admixtures are added directly to the concrete mix during batching, forming a hydrophobic barrier that prevents water penetration. Surface treatments, such as coatings and sealants, can also be applied to protect concrete from water damage. Additionally, installing a properly designed and installed drainage system can help manage water around the concrete structure.
When it comes to waterproofing concrete in commercial construction, it is crucial to work with experts who understand the complexities involved. Wells has extensive experience in waterproofing concrete structures and can provide tailored solutions to ensure the long-term durability and performance of your commercial building.
Expert Advice and Solutions from Wells
At Wells, we pride ourselves on our expertise in commercial waterproofing and our commitment to delivering innovative and quality solutions. Our team of service professionals provides consultation, recommending suitable solutions, and offering assistance during the installation process. We understand the unique challenges of commercial construction and can help you navigate the complexities of waterproofing to achieve optimal results. Contact Wells today for personalized advice and assistance with your commercial waterproofing needs.
Importance of Professional Commercial Waterproofing Services
Inadequate waterproofing can lead to extensive damage, costly repairs, and compromised structural integrity. By choosing professional commercial waterproofing services, you benefit from the expertise and experience of trained professionals who understand the intricacies of waterproofing commercial buildings. This investment not only protects your property but also provides peace of mind knowing that your building is safeguarded against water infiltration.
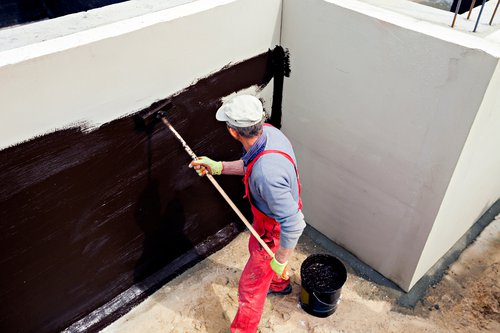
Trust Wells to Protect Your Commercial Building
When it comes to commercial waterproofing, Wells is a trusted building solution partner. With our expertise, high-quality solutions, and commitment to customer satisfaction, we are dedicated to ensuring the longevity, safety and value of your commercial building. Learn more about our waterproofing services here.
Contact Wells today for further information, consultations, and to discuss your specific commercial waterproofing needs.