Delivering on a commitment to a sustainable future for our people, partners, and planet.
At Wells, we’re committed to continuous innovation and improving our practices to support a more sustainable future. To help reduce our environmental footprint, we’ve identified four key sustainability goals that we’re actively pursuing across all locations.

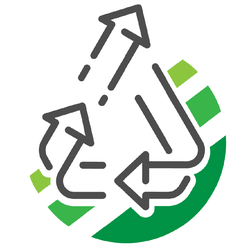
Reuse
Improving waste management through partner engagement and active team member engagement in recycling and reuse.

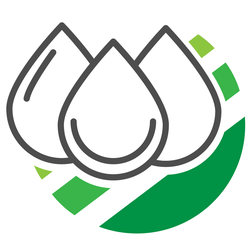
Water
Performing facility audits with a focus on water reuse, including mixer washouts, product rinsing, and yard utilization.
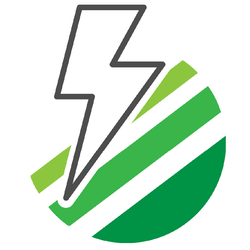
Energy
Performing facility energy audits focused on improving energy management and team member awareness.

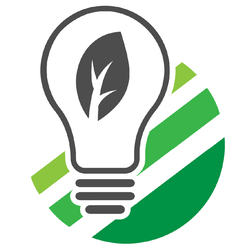
Mix
Advancing mix design through R&D and testing to reduce cement use by exploring SCMs, admixtures, and high fly ash blends.
A greener future ahead.
- Our manufacturing locations focus on optimizing mix designs by incorporating supplementary cementitious materials (SCMs) where possible, reducing embodied carbon while maintaining required strength and durability.
- We invest in extensive research and development to drive innovation in both our products and manufacturing processes.
- We conduct regular energy audits at all our locations to identify opportunities for improving energy efficiency and reducing consumption.
- A dedicated sustainability manager leads our strategy and ensures data accuracy for developing location-specific LCAs and EPDs, supported by a company-wide focus group that promotes sustainability and best practices.
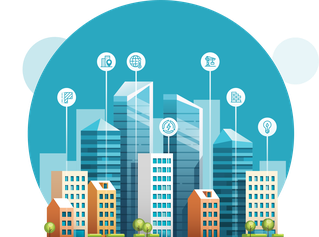

Environmental Product Declarations
Being transparent helps our design, construction and development partners feel confident they're building for a greener and healthier world when they use our building solutions. Wells believes in transparency in our design and manufacturing process, and we openly share current environmental product declarations (EPDs) upon request. Contact our team to get the conversation started on EPDs for your project.
Identifying better ways to build.
Our cladding system, Infinite Facade™, uses approximately 65% less concrete than typical precast spandrel construction in multi-story buildings. These lighter weight panels also help reduce the size of the structure needed to support the exterior enclosure, further reducing the overall embodied carbon impact.
We've also created an early design energy analysis tool to calculate potential EUI reduction and annual energy cost savings based on project design window to wall ratios.

Understanding environmental impact.
The green benefits of prefabrication.
Choosing a sustainable building solution involves more than just energy and material efficiency—it’s about long-term performance. Prefabricated concrete stands out for its durability, resilience, and recyclability, making it a smart choice for projects built to last.
Many sustainability assessments stop at cradle to gate—evaluating the environmental impact only up to the point a material leaves the factory. While this is important, it doesn’t tell the full story. Prefabricated concrete demonstrates its greatest sustainability advantages when evaluated cradle to grave—from raw material sourcing through production, installation, decades of service life, and eventual reuse or recycling.
Its durability, minimal maintenance requirements, thermal performance, and potential for reuse at the end of life all contribute to a significantly lower environmental impact over time. When you look beyond just the initial carbon footprint and consider the full lifecycle, prefabricated concrete consistently delivers long-term sustainability that many other materials simply can’t match. Learn more about the lifecycle advantage of prefabricated concrete.
Prefabricated concrete structures are built to last. With lifespans that often exceed 75 years, precast components significantly reduce the need for replacement, repair, and maintenance. This longevity not only preserves resources over time but also contributes to lower embodied carbon across a building's lifecycle—supporting a more sustainable built environment.
See how this long-term value comes to life in our featured longevity projects: American Family Field, Chester Fritz Auditorium, and Aurora Justice Center.
When it comes to climate-conscious construction, resiliency is key. Prefabricated concrete delivers exceptional strength and stability, making it ideal for withstanding extreme weather events, seismic activity, and temperature fluctuations. Precast structures outperform traditional building materials under stress, reducing long-term environmental and financial costs tied to post-disaster recovery and repair.
At the end of a building’s life, prefabricated concrete offers sustainable options far beyond demolition. Elements, like double tees, can often be deconstructed piece by piece, allowing for reuse in future structures or repurposing for infrastructure applications. If reuse isn’t feasible, the components can be processed and crushed to recover valuable materials such as aggregates and steel reinforcement for recycling. This flexibility not only reduces landfill waste but also supports a circular construction economy, giving second lives to the material.
Quick links on sustainability.
- PCI Comparative Life Cycle Assessment — Precast Concrete Commercial Buildings
- PCI Designer's Notebook — Sustainability with LEED v4
- PCI Designer's Notebook — Suitability of Environmental Product Declarations in Material Selection
- LEED to Federal Mandates: The Evolution of Sustainability in Construction
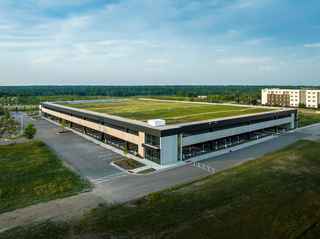