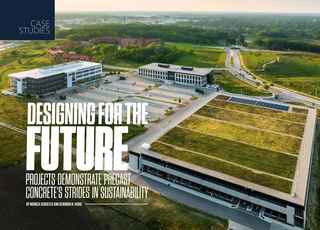

Case Study:
Innovation One Office and Parking
Wauwatosa, Wis. By Monica Schultes & Deborah R. Huso
Innovation One is a new three-story, 87,000-ft2 Class A office building in metropolitan Milwaukee, Wis., featuring desirable amenities situated in a serene setting. This multi-tenant commercial office space complements its natural landscape and provides a quiet workspace. There is a modern lobby, outdoor patio, common areas, tenant lounge, and fitness center. The neighboring total–precast concrete parking structure spans 177,000 ft2, holds 633 vehicles, and has a green roof.
The Innovation One campus prioritizes sustainable building and land development. The project achieved LEED silver certification as well as the distinction of being the first SITES-certified project in Wisconsin. When the project was completed in 2023, development firm Irgens moved its headquarters from downtown Milwaukee to help launch the new business park.
Certification Synergies
According to project architect Ryan Johnsen, associate principal at Kahler Slater, the owner was committed to pursuing both LEED and SITES certifications from the outset. There are some synergies between the two and they can be pursued either independently or in tandem. “The community at large was intent on a natural habitat,” describes Johnsen. “The area was rife with natural elements with a butterfly preserve and a large park across the street, so it had heightened scrutiny to create something sustainable and resilient,” he adds.
Despite the uncertain market for office space in many regions, the campus location is a big part of its success. Much of that resulted from the property surrounding the Innovation One campus with natural ponds, parkland, and protected butterfly zones. SITES-certified projects help reduce water demand, reduce stormwater runoff, enhance biodiversity, provide wildlife habitat, reduce energy consumption, improve air quality, and increase outdoor recreation opportunities.
Green Roof
Covering the entire footprint of the parking structure is the largest green roof in the state. The green roof is 4 in. deep and consists mostly of sedum and other native plants that require little maintenance. Viewed from adjacent structures, the green roof is an attractive addition to the skyline, but “the main goal is to absorb rainwater from the huge impermeable roof area,” describes Johnsen.
In addition to the aesthetics, the green roof provides environmental advantages as it soaks up stormwater to prevent flooding. The team worked with the Milwaukee Metropolitan Sewerage District, which is a regional water reclamation agency. The thirsty green roof helps to reduce the demand on the sewer system while providing a habitat for pollinators.
The roof also includes solar panels to power the parking structure itself. While the addition of soil, vegetation, and photovoltaic collectors added weight, no structural enhancements were required for the precast concrete structural components to support the extra load per square foot of the green roof.

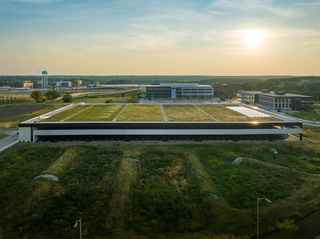

Precast Concrete Selected
Precast concrete was originally selected for both projects (office building and parking structure) for several reasons, says Doug Meidl, business development manager at Wells. The decision was based on economics, the qualities that precast concrete insulated panels bring to the project, and their (Wells’s) past performance with the owner/developer.
Johnsen agrees. “At the time, we selected precast concrete to be more efficient with the structure,” he explains. The year 2021 was a time of uncertainty in construction materials pricing. The project owner, Irgens, saw precast concrete as “an opportunity to build without compromising on quality or size.”
The building is a hybrid, with a precast concrete structure on the first floor with steel framing that continues on the floors above. The precast concrete slab provides a one-hour fire rating and also supports the stair and mechanical shafts. The first floor is partially below grade and contains parking, amenities, and office space. The second and third floors are office space.
Architectural Style
The building blends modern aesthetics with functionality. The exterior features architectural precast concrete insulated load-bearing panels with a simulated metal panel finish. The adjacent total–precast concrete parking structure integrates the same modern architectural design and sustainable features as the office building.
Johnsen recalls the design parameters. “Since the building is occupied by the owner/developer Irgens, they wanted to project a strong image and create an attractive building.” The design incorporates unique finishes on the precast concrete to emulate metal panels. The striking appearance is very dark in color and complements the small band of actual metal panels at the main entrance. “We wanted to avoid the appearance of an industrial building, so we were meticulous with the cladding system to ensure the color and texture had a high-quality appearance.”

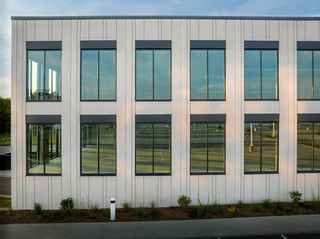
A closer look at the precast concrete insulated wall panels shows the reveal pattern that contrasts with painted bands that emulate a metal panel finish.
Casting
According to Meidl, the finishes are simple and elegant. The exterior design uses prefabricated architectural insulated load-bearing panels with two finishes. The first consists of white cement, light-gray pigment, and acid etching with reveals. The second were accent areas painted black to provide depth to the design and emulate the appearance of metal panels. When the mixture proportions were being developed, Wells experimented with several dark pigments to simulate a metallic finish. Because metal panels have a coated exterior, it was decided to paint the precast concrete panels in the field for a near-perfect match. The same process was used to cast the spandrel panels that clad the parking structure.
Daylighting and Thermal Mass
The façade of the office building includes expansive window configurations and clean geometric lines. The structure features f loor-to-ceiling glass for natural daylighting. Johnsen says, “We maximized the glass and minimized the concrete as much as possible.” Views from the office spaces are important and both LEED and SITES rating systems encourage natural light as well as being in and around nature. “Site orientation has a lot to do with solar gains, which is not as critical in our northern location in Wisconsin,” describes Johnsen. “We used high-performing, double pane windows and low-E [low-emissivity] coatings to reduce heat gain and improve energy performance.”
The panels have 4 in. of closed cell insulation, providing both the building envelope and vapor barrier in one piece. In colder climates, keeping the insulation outside of the weather barrier is preferred. The thermal mass of insulated precast concrete shifts the peak heating and cooling loads to help reduce mechanical system requirements and energy consumption.
Precast concrete insulated walls allow flexibility on the interior finish. “Some tenants prefer the industrial look of exposed concrete,” says Johnsen. Most tenants will opt to install drywall for a more traditional office space.
With the largest green roof and the first dual certification, the Innovation One office building and parking structures set the bar for sustainable construction. Together, the projects reduce water demand, reduce stormwater runoff, provide wildlife habitat, and reduce urban heat island. With LEED and SITES certifications, owner/developer/tenant Irgens demonstrates their commitment to building the best solution for their community.

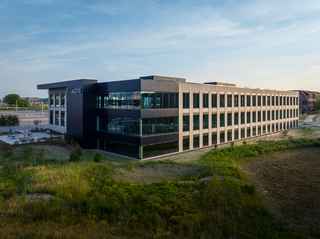

Project Details:
Location: Wauwatosa, Wis.
Architect: Kahler Slater, Milwaukee, Wis.
Owner: Irgens, Wauwatosa, Wis.
Contractor: CG Schmidt, Milwaukee, Wis.
Engineer: Pierce Engineers, Milwaukee, Wis.
PCI-Certified Precast Concrete Producer: Wells, Valders, Wis.
Precast Concrete Components: office building: 76 architectural insulated walls, 187 hollow-core slabs, 16 beams, 16 columns; parking structure: 128 double tees, 5 hollow-core slabs, 50 beams, 15 columns, 12 solid wall panels, 28 spandrels, 10 shear walls, 9 stairs
This article was originally published in PCI Ascent Winter 2025.