A central hub for North Loop.
North Loop Green in Minneapolis, MN, is a 34-story multi-use building with 354 luxury rental units, 96 short-term rental units, 17,000 sq ft of ground-level retail and dining space, 14 stories of office space, underground parking, and a one-acre park – all directly across the street from Target Field. This structure adds to the already bustling area of North Loop, providing the neighborhood with a variety of desired urban luxury amenities and shared experiences.
The architectural panels are horizontally orientated, and include reveals, creating a consistent pattern on the high-rise exterior facade. With a 7-inch depth, each panel frames a series of windows that are recessed into the cladding. A large part of the pre-design focused on where the windows would lie within each panel since the windows are field installed and insulated. By optimizing the panel design, each window avoids a cold spot gap, improving insulation, and energy-efficiency, while reducing condensation build-up.
NAIOP Minnesota 2024 Award of Excellence - Mixed Use
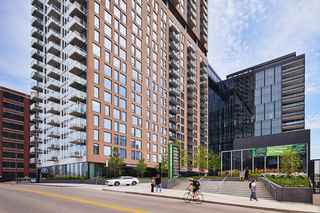
Using a mix of building systems, floor-to-ceiling glass windows line two opposite sides of the residential full-concrete structure, while prefabricated architectural panels clad the other two sides. When bringing a multi-family residential building to life, prefabricated building components bring value in various ways. The project developer chose Wells precast architectural panels in a red-brown etched finish that matched the rest of the surrounding structure well. Additionally, precast is durable, more cost-effective and provides more sound deadening than a total-glass finish and can be erected in a very short amount of time. Particularly in a busy urban downtown area with high traffic and a limited site footprint. Prefabricated building components are manufactured off-site and shipped in only when needed, avoiding the need for space to store near construction.
Overcoming challenges.
It takes a team of skilled experts to construct a quality building. During construction, the building had protruding concrete slabs to form future balcony patios along with multiple exterior lifts to bring workers up and down the building. As the building went up, subcontractors began working on the lower levels. The Wells field crew had to be especially careful as to not let any of the precast panels collide with the patios or lifts, which would have resulted in damaging the panels. Additionally, some of the panels had to be maneuvered and installed between the two lifts, with only an inch of open space on each side. The crew successfully communicated with the crane operator through all phases of the project to avoid any installation mistakes.
Constructing a large building in the middle of a bustling urban area requires strict planning and a demanding schedule. The general contractor provided two large tower cranes for the project and to ensure North Loop Green remained on schedule, the Wells team worked a unique shift from mid-afternoon to nearly 10pm each working day while the other trades worked from dawn until mid-afternoon. This two-shift schedule allowed the cranes to be utilized all day for the different needs of each project partner.

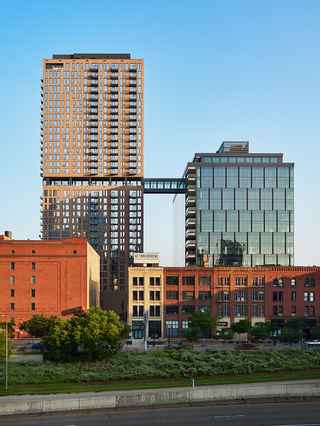
To avoid unnecessary issues on-site, Wells manufacturing facilities have pre-built frames that simulate the construction dimensions of any potential building, with the ability to change heights and widths as needed. The prefabricated panels can be temporarily installed on the frame and mocked up to show how the panel will be connected to the side of the building. Each panel is tested to fit within the building dimensions and connections are verified there is no interference while mounting. This testing ensured that once the panels were shipped to the North Loop job site, there were not any issues when installing – guaranteeing quality and ensuring the project remained on schedule.
Thirty-four stories of sealants and firestopping.
In addition to the 90,000 sq ft of architectural wall panels, Wells also provided the structure’s precast joint sealants and slab-edge firestopping. A necessary step in any precast installation is sealing interior and exterior panel joints. Wells Sealants and Restoration team utilized Sikasil 290 for the exterior joints, a silicone sealant that performs well under UV exposure and is resistant to external weather conditions – necessary for the harsh Minnesota seasons. The interior joints are sealed with Manus-Bond 75-AMC, which is a paintable and fast-curing joint sealant that has excellent flexibility and is compatible with the firestopping products used. Both joint sealants are soft and pliable, which is necessary for a tall building that will undergo constant movement.
Firestopping was performed on the slab-edge space of each wall panel. Wells installed mineral wool made from natural stone fibers, a non-combustible material that prevents fire from jumping floor to floor. Additionally, using silicone on the top side of the slab-edge joint prevents the passage of smoke and hot gases into the occupied space above.
Due to the placement of the structural concrete columns, slab-edge firestopping was not possible in the corners of the building. With the help of Hilti (a construction tool company), an engineering solution was designed to encompass the vertical joints between the columns and the back of the precast to maintain the continuity of the 2-hour fire rating.
Because of the dual-phase exterior system, the sealants’ lifespans are lengthened, benefiting the owner of the building. Wells installed an internal and external bead on the exterior space of the panel with a very small air gap – allowing any condensation to drain out. Additionally, the sun exposure that the exterior faces is very harmful to a building over time. Utilizing a dual-phase exterior system, the UV exposure is spread out so one bead does not take the entire brunt of the exposure.
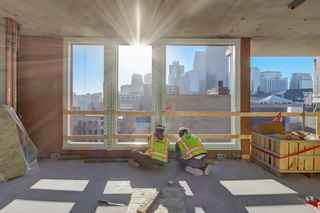

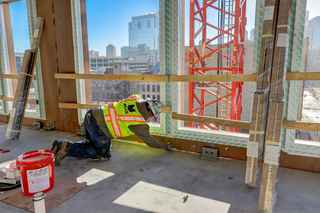

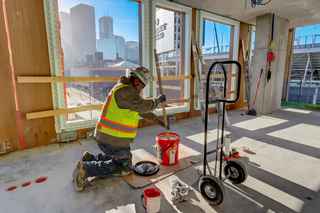
Here to stay.
North Loop Green is a prime example of the exceptional skill and expertise needed to construct a high-rise building and showcases the benefits that Wells prefabricated building systems and services provide. North Loop Green has become prime office, residential and retail real estate and a staple of downtown Minneapolis and the North Loop community.
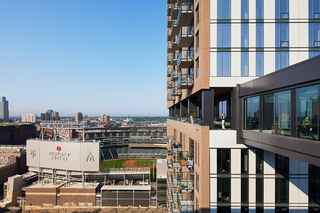

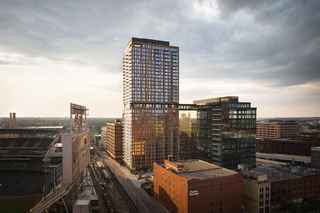

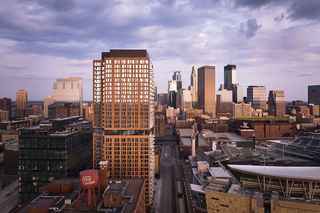