Meeting Colorado’s regional demand.
With a ground floor of 823,000 sq ft and 664,000 sq ft on each of the four floors above, this 5-story, 3.48 million sq ft Colorado-based warehouse and distribution center is one of the largest in the nation. The center is planned to employ over 1,000 individuals that will work alongside robots, improving processes to meet the increasing customer demands of northern Colorado.
Initially, the general contractor was looking into using site-cast tilt-up concrete panels for the building. Ultimately the contractor and owner chose Wells building solutions due to a significantly shorter construction schedule and overall better value. This decision was made post-design, so Wells engineering and design team converted the design from site-cast to prefabricated walls.
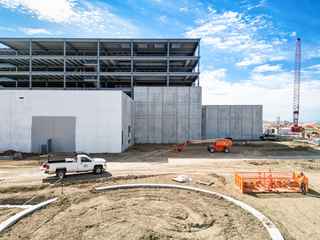
Wells provided the exterior wall system for this monstrous structure, utilizing over 175,000 sq ft of structural insulated and structural solid walls. The extensive wall panels reach 40 feet tall, covering the building exterior from the ground level to the third floor, while metal panels cover the remaining floors. The wall panels feature a smooth gray concrete finish with embedded reveals and were field painted to the owner’s branded colors. The front of the building incorporates a formliner finish to enhance the entrance and provide a more unique aesthetic where the most traffic passes by.
Creating a massive structure comes with its challenges. The building structure is comprised of steel; usually during construction prefabricated wall panels are installed first, and the steel structure is built within the panels. However, to expedite the schedule with this project, Wells worked closely with the steel erector to sequence the work along with their work — the steel was installed, and the precast panels were installed immediately after, tying back to the steel until it was sealed. The Wells erection team collaborated with multiple trades to stay on track with the completion date.
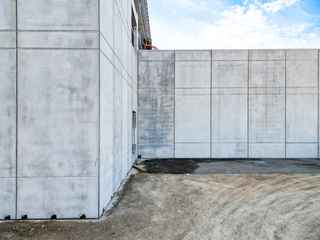
Wells Sealants and Restoration team rounds out installation.
Wells’ full-service Sealants and Restoration team played a large role for this project, as joint sealants are a necessary part of any precast erection to ensure the panels are connected and sealed from the external environment.
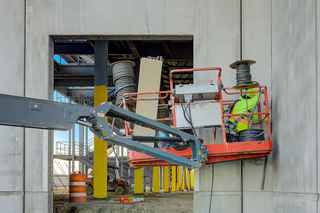
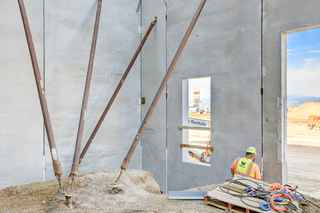
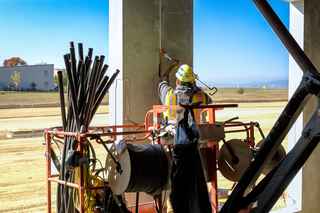
The interior joints of the wall panels utilize a MasterSeal NP 2 urethane caulk a very flexible sealant, so if the warehouse experiences any slight structural shifting and settling, there is less of a need for caulking repair. The urethane caulk involved mixing components together and then applying using a bulk gun. Since the mixture hardens quickly, our team efficiently applied the compound to the joints while still providing a neat finish.
The exterior joints use Dow 790 silicone and are applied with a caulking gun. Although less flexible than the interior caulking, this type of sealant holds up better against UV light and resists harmful sunlight, rain, snow and extreme temperatures, making it the best choice for exterior joint sealing. Wells utilized a variety of colors for the external caulking to match the building design and color scheme. Out of the four colors the owner chose, two were custom blends that our Sealants team mixed to the correct color.
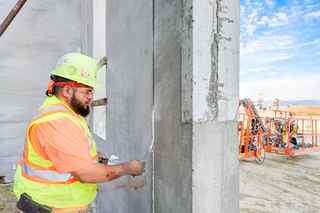
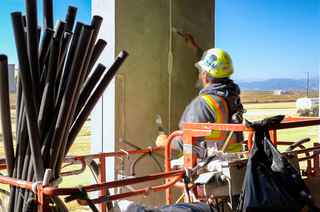
Since the immense distribution center was framed with steel, there were significant challenges with accessibility to some of the joints. The entire project required close to 35,000 linear feet of caulking, and a portion of the joints requiring caulking were blocked behind the metal frame. To overcome this building challenge, the Sealants team used creative solutions like longer extension tubes to apply the caulking. This solution ensured that there were no joints left unsealed and the construction schedule could continue unhindered.