What is total precast?
Total precast buildings utilize the full array of Wells building solutions, comprised of structural and architectural prefabricated building components. Utilizing precast for the entire building solution — from floors to walls to stairways to the building enclosure — makes a long-lasting and durable structure that can stand the test of time. Wells has extensive expertise with total precast designs for a variety of market segments, and you can feel confident using Wells as your single-source building solutions provider — simplifying your project from start to finish.

Architectural Building Components
The exterior of a total precast structure utilizes architectural load-bearing precast walls. With prefabrication, endless architectural aesthetics can be achieved while remaining durable and resilient.
Structural Building Components
The structure of a total precast building is comprised of structural precast components, including beams, columns, hollowcore, stairs, walls and more.
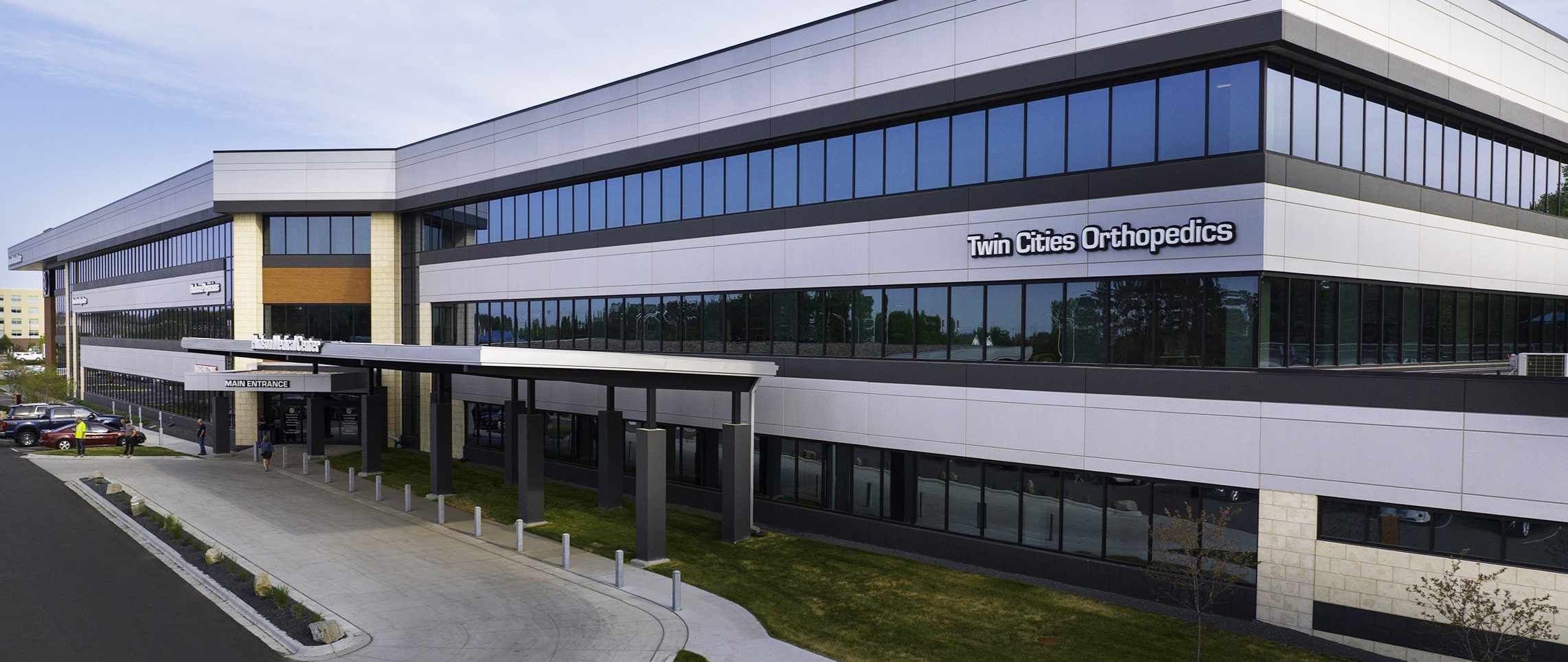
Total precast structures protect your bottom line.
Total precast structures benefit the entire construction team, from the architect to contractor to engineer to owner. From load bearing wall panels to comprehensive design and support, combining Wells structural and architectural building solutions provides benefits for all.
Benefits of Total Precast
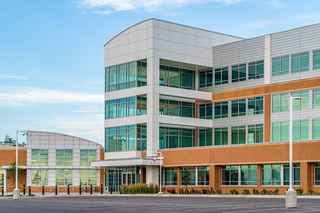
Total precast buildings offer several benefits across various geographic regions and market sectors. Key benefits include:
- Accelerated construction
- Durability/resiliency
- Aesthetic versatility
- Noise reduction
- Lower project cost
- Minimized site disturbance
- Energy efficiency
- Just-in-time delivery
Total Precast Benefits for Architects
Aesthetic Variety: There is a wide array of color and finish options when using precast, including thin brick, sandblast, acid etch, waterwash, custom formliners, Graphic Concrete, and virtually any color.
Comprehensive Design & Drawing Support: We have in-house drafters and engineers that will work side-by-side with you as the drawings and projects progress. This makes for a seamless transition from a napkin sketch to 100% construction documents.
Total Precast Benefits for Contractors
Core and Shell Under One Trade: This reduces the number of individuals involved in the building process.
No Staging Required: When a precast panel shows up on a jobsite, it is taken off the truck and put into its final position on the building. This avoids congestion on-site and ultimately makes for a safer jobsite.
Total Precast Benefits for Engineers
Load-Bearing Wall Panel Systems: A load-bearing wall panel system, combined with the fact that precast double tees can span up to 110 ft, eliminates the clutter (and cost) of extra columns and beams on the interior of the building.
Comprehensive Design & Drawing Support: In-house engineering can work side-by-side with the EOR to develop the proper component sizes for the loading indicated.
Total Precast Owner Benefits
Speed to Market: Being able to produce a structure year-round in our climate-controlled manufacturing facilities allows for a faster construction schedule.
Reduced Life Cycle Costs: Precast is low maintenance and has a 100 year life span
Total Precast Building Solution Examples
Total Precast Resources
Featured total precast concrete projects.
View more Wells projects.