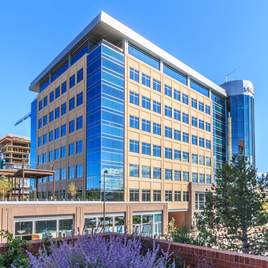
Denver, CO
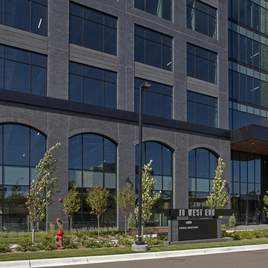
St. Louis Park, MN

Award Winner
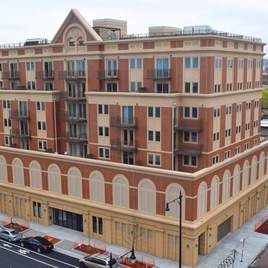
Chicago, IL
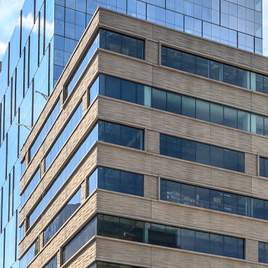
Denver, CO
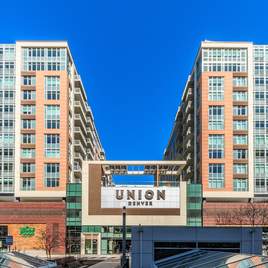
Denver, CO
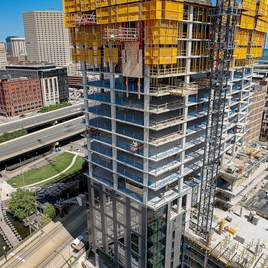
Milwaukee, WI
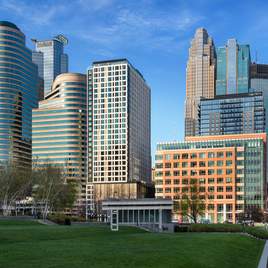
Minneapolis, MN
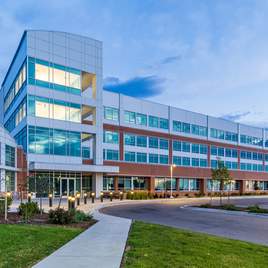
Confidential, CO
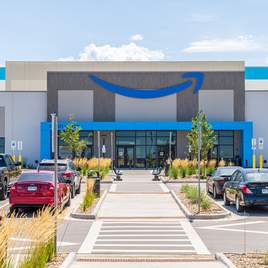
Aurora, CO

Award Winner
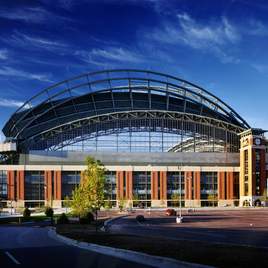
Milwaukee, WI
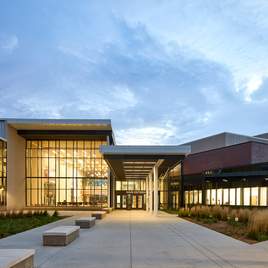
Ames, IA
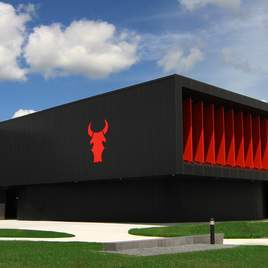
Arden Hills, MN
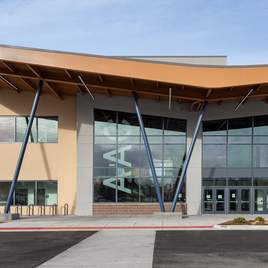
Arvada, CO
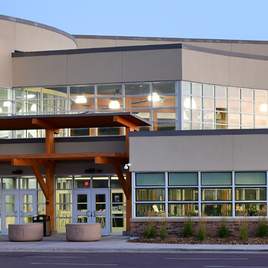
Ashland, WI
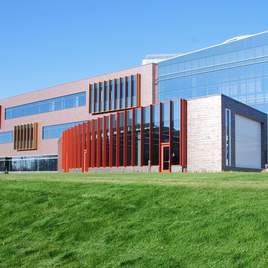
Minneapolis, MN

Award Winner
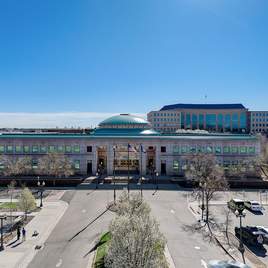
Aurora, CO
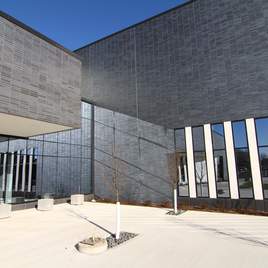
Austin, MN
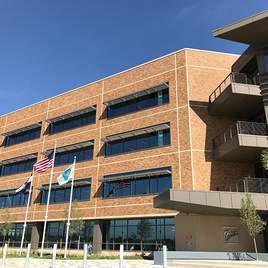
Westminster, CO
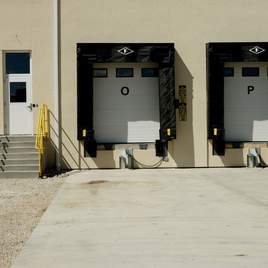
Freedom, WI
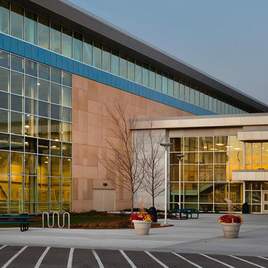
Woodbury, MN
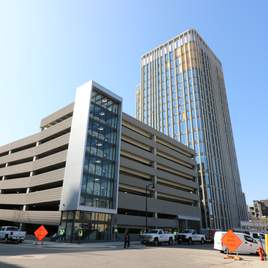
Fargo, ND
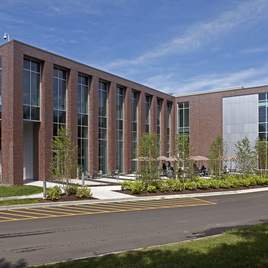
Maple Grove, MN
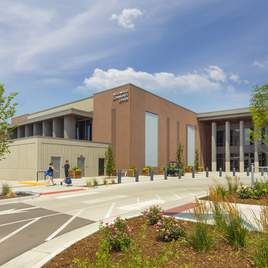
Broomfield, CO
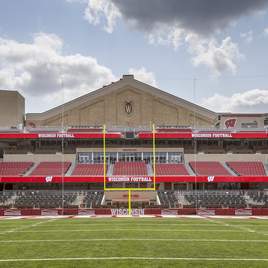
Madison, WI